Pebble Clutch Jug
Couldn't load pickup availability
For many years I went to the Scilly Isles quite regularly, camping with family and friends and occasionally staying in cottages or, on a few rare occasions, in the New Inn. There were, even then, a few special areas...around the back of Bryher there is a small bay called 'Stinky Bay" - maybe that's just my name! A perfect rock for sitting against, watching seals and a lovely little bay with the most perfect sea-rounded white boulders and pebbles. This range might be obvious in its conception but trying to hand make a form that has the same tacticity (is that a word?) as a rock that has been smoothed for eons by the ocean can be a challenge. But it is too easy to say that the range was inspired by just one beach, Solva in Pembrokeshire sticks in my mind. Lee Bay, Kilve, Lillestock also inspired me. Beaches are amazing and have been a constant source of inspiration - maybe it's the sea air clearing the cobwebs out....
Like most of my pieces, these start with gathers of clear glass. I have a furnace which I keep at 1040 c constantly, it has a crucible inside which holds approximately 140 litres of molten glass when it is full. To start a piece, you need a hot blowing iron, this is the dipped into the molten glass and turned much like winding honey onto a spoon (a gather) If you need to make a larger piece you have to centre the gather ( make it on the same axis as the iron) let it cool before re-dipping the iron in the furnace. This is repeated until you have the amount of glass required, two gathers is generally a medium piece. The gathering size is determined by eye. Once you have the required amount of glass, the gather or parison is rolled through white (or whichever colour you are using for the background) powdered glass frit to coat the surface. Your assistant meanwhile has gathered a small amount of glass on a solid iron and has rolled it through the powder for the trail colour. Both pieces are heated to melt the powders in, the trail is heated up more than the base colour and then the trail is wrapped around the piece over the end and round the middle. This is then all heated up and the parison is now dipped in the coloured chips which have been arranged on another metal table (marver) Again the whole piece is heated up, shaped and finally blown into its final form. Once I'm satisfied, the piece is transferred to a punty iron before the top is heated and finished.
The final piece is then put into a kiln that is kept at a constant 500 degrees all day. This is ramped down overnight to anneal all the glass I have made during the day. The next morning when the work is cold, we finish the pieces off and sign them.
Nearly all my glass is made to be used, but maybe jugs are an exception......I have always liked the dichotomy of form and function, art and craft etc. You can use these jugs, I make them to feel good in the hand, they are incredibly tactile........ but I can not guarantee drip free pouring. Sorry.
Matt finish. Height 125 mm width 110 mm depth 80 mm
Share
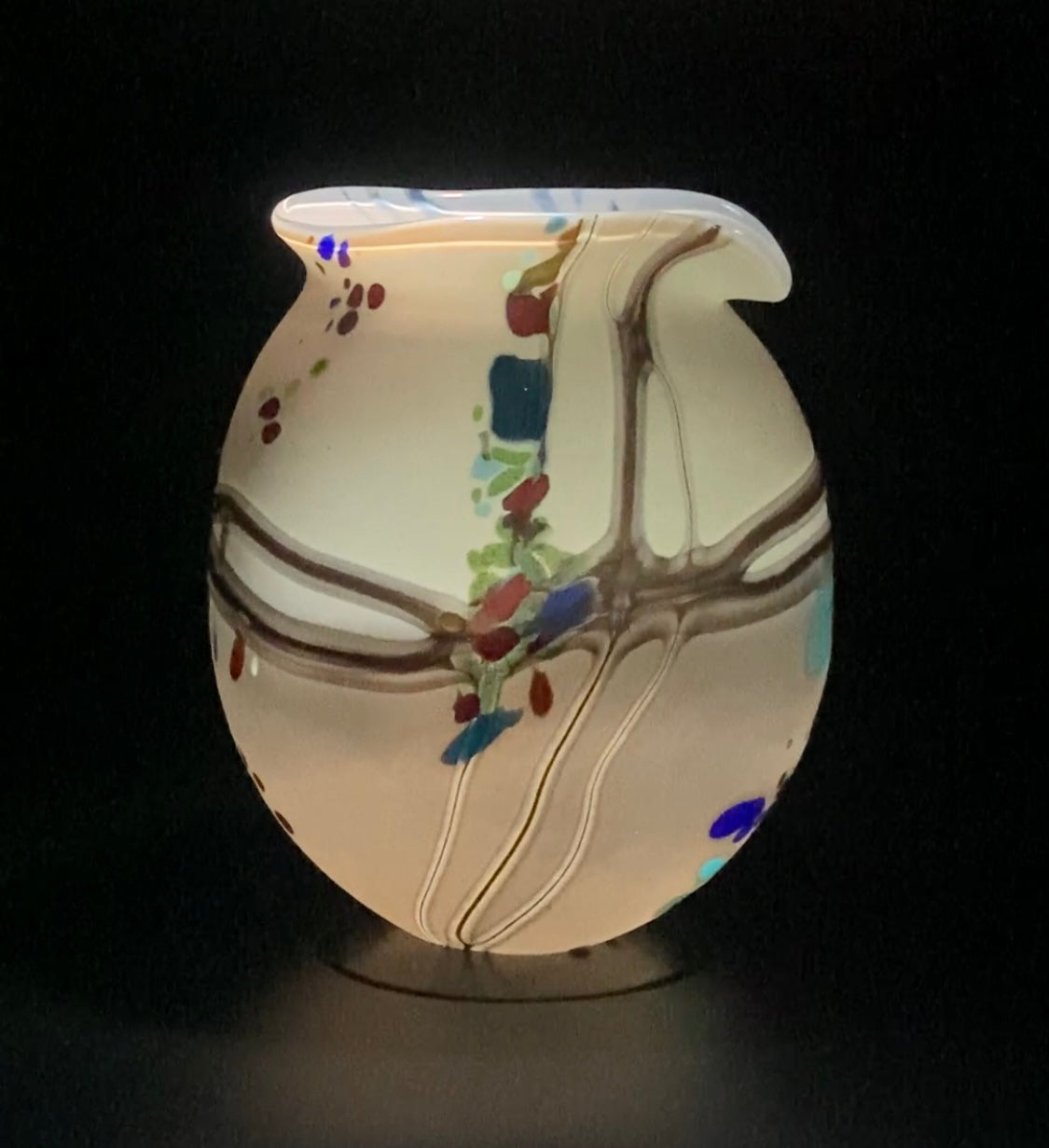
Subscribe to our emails
Subscribe to our mailing list for insider news, product launches, and more.